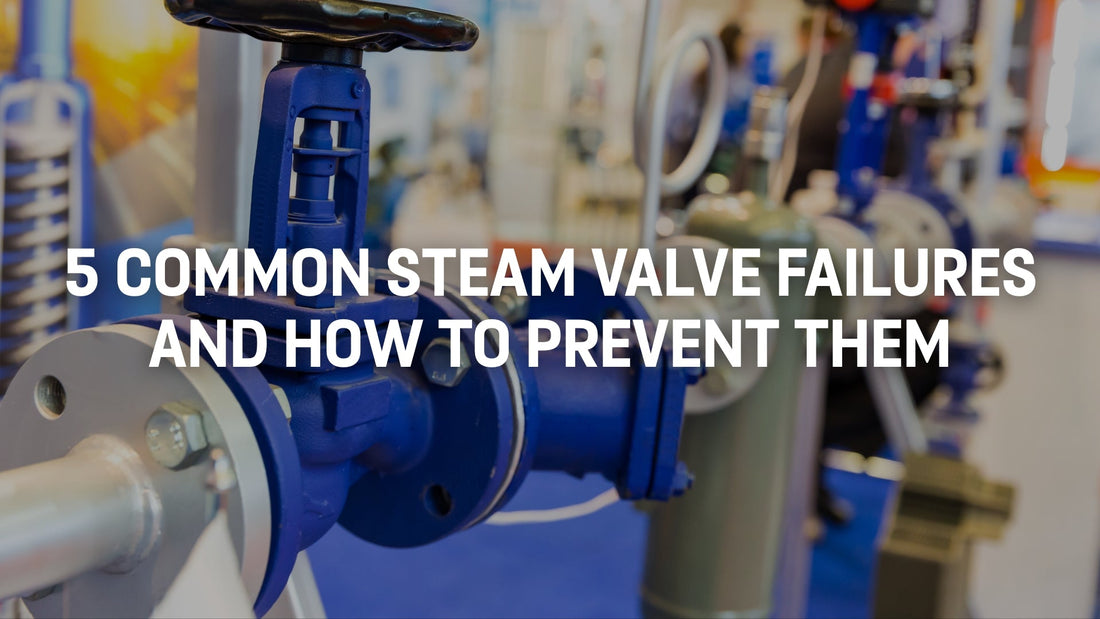
5 Common Steam Valve Failures and How to Prevent Them
Share
đź”§ Key Points
Discover the top 5 most frequent steam valve failures
Learn how to prevent costly breakdowns and downtime
Improve efficiency and safety across your steam system
Tips from industry experts in steam valve supply and servicing
When dealing with high-pressure steam systems, valve failure isn’t just inconvenient—it can be dangerous and expensive. At Steam Valves UK, we’ve seen firsthand how common faults can cause significant disruption. In this blog, we break down the five most common steam valve failures and share practical ways to prevent them before they impact your operation.
1. ⚠️ Leakage Around the Valve Seat
The Problem: Internal leakage is one of the most common failures in steam valves. Over time, wear and erosion of the valve seat or disc allows steam to pass through even when the valve is closed.
The Fix: Regular inspection and seat replacement are key. Using high-quality spare parts such as TTV Butterfly Valve Silicone Seats can dramatically reduce the risk of internal leaks. Ensuring proper alignment during installation also prevents premature wear.
2. đź› Sticking or Seizing Valve Stems
The Problem: Steam can cause scaling and corrosion, particularly in older valves or those in harsh environments. This leads to stiff or seized valve stems that affect operation and control.
The Fix: Routine maintenance and proper lubrication go a long way. Specify valves with stainless steel stems or coatings that resist corrosion. Consider actuator upgrades or positioners for smoother control.
3. 🔥 Thermal Expansion Damage
The Problem: Steam systems operate at extremely high temperatures. Without the right clearances, valves can suffer from thermal expansion damage—cracking, jamming, or breaking under pressure.
The Fix: Select valves engineered for steam applications from trusted brands like ARI Armaturen and Samson. These are designed with thermal dynamics in mind. Always allow for heat cycles in system design and install expansion joints where needed.
4. đź’§ Condensate Build-Up
The Problem: Improper drainage or failed steam traps can allow condensate to collect inside the valve, causing water hammer, pitting, and internal component failure.
The Fix: Install reliable steam traps such as the ARI-Condensate range and regularly test them. A dry steam line is a healthy one. Include strainers upstream to prevent debris from impacting trap performance.
5. â›” Incorrect Valve Selection
The Problem: Using the wrong valve type, size, or material for a steam application is a recipe for failure. Undersised valves can restrict flow, while unsuitable materials may crack or corrode.
The Fix: Work with a steam valve specialist who understands system pressure, temperature, and media. At SteamValves.co.uk, we help you choose the right solution—whether it’s a Globe Valve, Ball Valve, or Butterfly Valve—tailored to steam applications.
Final Thoughts đź’¬
Steam valve failure isn’t just about faulty parts—it’s often a result of neglected maintenance, poor specification, or lack of system insight. By identifying these common issues early and choosing trusted products from leading manufacturers, you can extend the life of your system, reduce downtime, and ensure safety across the board.
đź’ˇ Need expert advice or fast replacement parts? Contact Steam Valves UK today and speak to our technical team.
Want more steam valve insights? Head over to steamvalves.co.uk to explore our full product range and support services.